[url=]关键词:[/url]精益生产,TPM,5S,薪酬与绩效,班组长培训 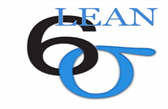
实施精益生产的重要一步是消除质量不良引起的浪费,仔细分析现场质量不良的现象,我们可以发现大多数生产现场的不良可以归为两类。
一类,我们可以称为管理性不良,比如,漏错装或贴错标签或螺丝没有紧固等,其产生的原因多半是因为作业者疏忽或不熟练,或基层管理不足,生产物料组织方式混乱导致。
另一类,可称为“痼疾性”不良,这一类不良表现为长期反复发生,不良率水平维持在某个水准,无法彻底根除或迅速减少。其产生的根本原因很复杂,很有可能是现有工艺技术自带的缺陷,比如研磨或喷涂会产生异物,或设计结构复杂对某些零部件精加工水准,配合程度要求较高等。消除这两类不良应该有不同的方针策略。 
对于管理性不良,我们认为应该以现场作业者和基层管理者为主体展开QC小组活动,运用丰田的实际问题解决或称A3的方法,持之以恒的通过记录观测数据,分析原因并及时反馈,点检标准,员工技能强化和5S活动等,以“零缺陷”为目标彻底的消除。
而对痼疾性不良,则应组成有更多力量参与的攻关小组,小组成员包括现场工作人员,工程技术和产品开发的工程师,供应商甚至客户在内。对痼疾性不良发生的根本原因,需要改进的工艺或强化控制管理的节点,进行彻底的把握,开发出新的工艺或强化人员的工作技能。比如,三星公司为了克服工艺过程中异物的混入,会采取从集团层面在每个工厂设立“异物管理士官训练营”等措施。我们认为6sigma的解决路径和众多工具对“痼疾性不良”的降低有更大的贡献。
其实,无论是QC活动,A3还是6sigma的DMAIC,它们都是遵从的PDCA的工作方法论,追求的是对品质问题根本原因的查找和对策。
http://www.tpm123.com http://www.szkaizen.com/#/fashion
|