冲压工序往往是推行精益生产最艰难的部门,而作为批量生产的典范,其问题也是最突出的部门: 不仅工序间大量在制品库存: 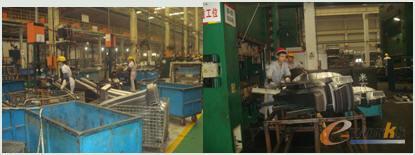
冲压车间的成品库,也是公司库存资金和场地占用的大户:
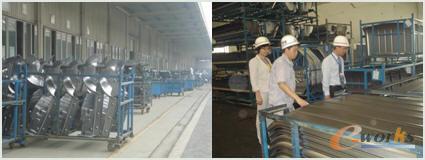
作为精益生产的顽固分子,其有更多理由拒绝单件流:设备布局很难改变、不同产品需要冲压设备的吨位不同,切换时间很长等等,还有一个很主要的原因先导者很少,运用得案例很少。 而这一周在给某汽车零部件企业培训辅导时,看到了一个冲压单件流的成功案例: 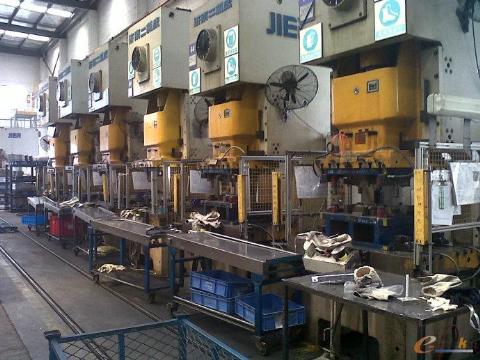
冲压车间有好几条单件流生产线,不同生产线设备吨位不同,正好铸件产品大小与设备吨位也有某种正相关,因此将产品划分价值流就不难了。
据工程师介绍这种模式已经很多年了,在这种模式下运行,其工艺标准化是一大挑战。该工程师分享了一个案例: 一次一种新产品需要9道工序完成,但设备流程只有7道,为了符合流程运转,不仅公司内部的工艺进行了调整,而且邀请供应商进行调整,最后实现了符合要求的工艺方法。 这个案例不仅展现了冲压的单件流,也很好的分享给大家工艺标准化是完全能够做到的,很多工艺方法和工艺条件是可以改变的,在满足客户“价值”的前提下有很多工艺实现的方法。 而采取什么思路设计工艺才是关键和决定因素,为了让工艺设计的工作简单还是为什么生产流程简单、好管理、生产效率高、成本低?当然,成本是指综合成本,而不是某道工序或某个环节的成本。 分享此案例,希望能有助于一些企业对精益生产最后堡垒的攻关。
|