1995年,御手洗冨士夫开始担任佳能集团的社长,并主导了一系列革新,但是关于生产的革新并不容易。最早给佳能集团带来“单元生产方式”想法的是一家到长浜佳能参观的一家电子零部件工厂。这个电子零部件工厂根据长浜佳能的管理者的“要求”,不客气地指出,长浜佳能的最先进的自动仓库、传送带、无人帮运系统等耗费巨资的设备贬得一文不值。“佳能是有钱的大公司,这些长长的传送带根本就没必要”,“把‘无人帮运’这种无聊的东西都合理化了,象这样蠢的事再也找不到第二件了。”受到了这样的刺激,长浜佳能感到“一定要做点什么进行改革了。” 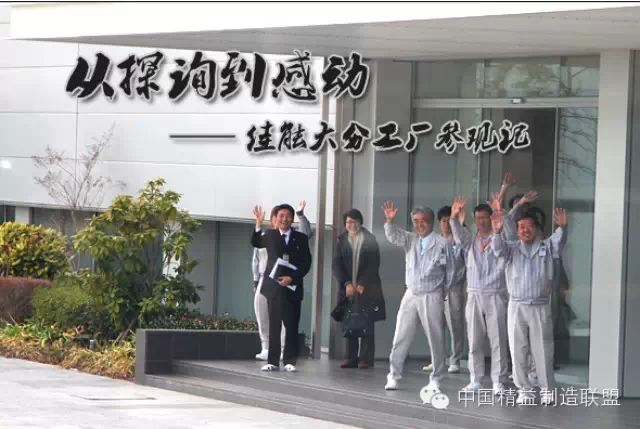 两个月后,佳能社长御手洗冨士夫以及各位董事一起考察了讽刺过佳能的那家电子零部件工厂以及一家大型电机制造工厂的子公司,发现它们已经停止了传送带流水作业方式,采取了一种新的被称为“单元生产”的生产方式——由几个人组成的生产小组从事全部复杂工程,生产出完整产品。在这里,传送带已全被单元生产方式所代替。在参观完工厂后,御手洗冨士夫决定从长浜佳能开始进行生产革新。1998年初,革新运动正式开始。  长浜佳能关于单元生产方式的革新努力,首先在相对简单的激光扫描仪生产上试验。试验的负责人武藤和山田将6条生产线中的一条一条依次进行变更。他们将生产线改成10个人组成一个小组进行作业。试验开始得并不顺利,从各种数据看,生产效率不仅没有明显地提高,反而降低了。但是“救命女神”最终出现了。生产现场的女工组成了一个10人女性生产小组,她们在每次作业结束后,自主地召开一个小型的讨论会,摸索改善的方法。与此同时,现场生产的工人们尽管有所不满,但也渐渐地熟悉了这种作业方式,生产现场开始出现工人积极工作的氛围。在连续召开三天的讨论会后,女性生产小组终于提前完成了生产任务,受到她们的激励,其他现场的工人也开始积极地投入工作。 到这里,我们再来分析一下单元生产方式相对于流水线生产方式的优势。 首先,就是它对生产规模有更强的灵活性。流水线生产方式最适合大规模生产,对于小批量、多品种生产没有效率优势。而今天企业所面临的市场情况恰恰不是少品种、大批量,而是更显著的客户个性化需求导致的多品种、小批量,企业在技术及产品创新上的竞争也加剧了这一趋势。事实上,单一品种的生产在亨利·福特时代的后期就已经行不通了,福特本人最终也放弃了只生产一种T型车的政策,被迫转而生产多几种车型。20世纪末,小批量、多品种的趋势更加明显。显然,单元生产方式相比于以传送带为特征的流水线生产方式更能适应小批量、多品种的环境。如果客户的订单批量下,那就由一个或少数几个单元生产就可以了,如果客户的订单批量大,就多增加几个单元以提高生产能力,非常灵活。 其次,生产所需要的设备投资大为减少。尤其是相对于日本企业一贯追求的机器自动化,单元生产方式以人和通用工具(例如那些“机关”)为主,只需要很少的设备投资,就可以满足各种生产的要求。这一点在御手洗冨士夫看来非常重要,非常符合他强调的“现金流”经营,要保持良好的现金流,当然应该少把先进投入到那些难以变现的、昂贵的、重厚长大的自动化设备上。 第三,从工业工程专业的角度看,单元生产方式由于工序的分解比传统流水线式生产时的分解要粗得多,不必为了追求分工的专业化效率,但是可以换到分工的更加均衡,也就是流水线生产的“平衡率”的提高。也就是,尽管专业化分工的效率有所下降,但是协作的整体效率却可能提高。更何况,流水线生产方式下过细的工序分解经常会把本来有机连结在一起的、流畅的动作组合强行拆开以迎合“节拍”的需要,单元生产方式可以最大程度地避免这种生硬的“分解”。 第四,单元生产方式下,作业者需要做较复杂的操作组合,而不是原先很简单、重复性的枯燥操作,使得作业者工作的趣味性提高,更重要的是,单元生产方式的实施往往需要作业者小组一起自己研究如何更好地工作,每个作业者从中体会到的参与感、挑战感和满足感是在流水线式生产方式下不可能体会到的。就像长浜佳能的“救命女神”生产小组一样,她们每天下班后自发地举行讨论会,研究如何改善工作。当然,通过主动地参加研究如何改善工作,工人们得到的技能提升也是非常显著的。正是在这个意义上,一些媒体认为,单元生产方式将原来流水线生产方式下的“片面人”变成了“完整人”,带来了工业社会生产线上“人”的复归。 第五,单元生产方式下,因为传送带不再需要了,而节省了面积。福特很强调传送带对流水线生产方式的重要性,并将它作为三个主要原则之一,因为它替代了原来耗费人的时间、力气的搬运活动。但是在单元生产方式下,工作台的面积并不大,作业者们围坐在工作台四周,每个作业者装配后的在制品被放在他很方便的地方,通常是由前方,而处在他的下一道工序的作业者也可以很自然地、方便地拿到。因为搬运的距离完全在每个作业者手臂够到的方便的范围内,也就根本不再需要传送带来完成搬运。与传送带相应的无人帮运系统也没有什么用武之地了。 正如前面解释的那样,“单元生产方式”并不是佳能集团首创的。此前,在提到的电子零部件厂及其他一些企业中已经率先使用了“单元生产方式”。此后,日本很多企业都开始采用单元生产方式。松下在静冈的工厂采用单元生产方式实现了手机月产能100万台,也是单元生产方式方面一个著名的成功案例。但为何“单元生产方式”被作为佳能革新的最重要内容之一呢?而且为什么佳能采用单元生产方式最为有影响呢? 之所以“单元生产方式”与佳能集团被联系得如此紧密,以下原因是不能被忽视的。 第一,单元生产方式在佳能确实取得了成功,而佳能在此期间也取得了巨大的成功。由于以采用单元生产方式为代表的制造革新,以及其他一系列革新,佳能的经营业绩连续大幅增长,成为世界瞩目的对象,并成为日本高技术、高利润企业的新代表。尽管采用单元生产方式是佳能取得成功的重要原因,但它并不是唯一原因,甚至也不一定是最重要的。但御手洗冨士夫祭出的“回国生产”这一说法非常有鼓动力,把“回国生产”与“单元生产方式”结合在一起,使得“单元生产方式”更有影响。不过,实际上,“回国生产”的动力很大程度是为了消化在“单元生产方式”革新中节约出来的“机动人员”,而采用的方式当然仍然是“单元生产方式”。 第二,长浜佳能在推行“单元生产方式”革新的过程中通过自己的实践取得了重要的经验,形成了自己独具特色的“三棱镜式单元生产”。“三棱镜”强调的是单元生产方式之所以在佳能取得成功,并不仅仅是某一方面努力的结果。如果仅仅有一个单元生产方式的模式,没有现场工人在生产现场挥汗如雨的勤奋工作,没有他们在工作中积累下来的无数经验,没有各个方面的群策群力,单元生产方式的改革是不可能进展得那样顺利的。 第三,佳能集团在很短的时间内,成功地把单元生产方式推广到集团内的每一个工厂。在长浜佳能单元生产方式试验取得成功后,仅仅两年的时间,在御手洗冨士夫的强力领导下,加上有长浜佳能的样板作用,通过“自下而上”、“自上而下”的结合,单元生产方式在佳能集团全面取得成功。而在日本没有哪家企业有这样的能力和速度。所以,佳能集团自然成为单元生产方式最好的形象代言人。“自上而下”,御手洗冨士夫的强力领导应该也是“三棱镜式单元生产方式”的一个组成部分。佳能集团不仅在集团内推行单元生产方式,而且也极力劝说客户企业采取这种方式,并乐于提供人员指导。 讲到佳能独具特色的“三棱镜式单元生产方式”,必须讲到公司为了推进革新所做的教育和训练方面的努力。长浜佳能在公司内部设立单独的“三棱镜式单元生产进修班”,工人们在正是投入单元生产之前,都必须接受专业训练,为了工人的进修,佳能还在公司内部培养指导老师。最初,佳能依靠的是从外面请来的顾问,到了后来,佳能自己的职员也成为老师,中途加入到培训班中,2001年,指导者的人数已经累计到达3000人。 五、单元生产方式对中国意味着什么? 单元生产方式是不是象一些人认为的那样,只适用于日本呢?中国企业能不能采用单元生产方式呢?若要在中国企业中面对这样的问题,我的看法是: 首先,单元生产方式在佳能的成功并不意味着单元生产方式已经可以全面取代流水线生产方式了。首先是单元生产方式并不是在生产效率上完全超过了流水线式生产方式,只是运用效率上较小的损失换来生产批量、品种上的较大灵活性,在小批量、多品种时体现出效率来。同时,单元生产方式相对于日本流行的机器自动化流水线方式,在成本、柔性方面有显著优势。在大规模生产的情况下,中国企业依靠劳动力成本优势进行流水线生产仍然是有效的一种方式,但在小批量、多品种的情况下不妨尝试单元生产方式。 其次,单元生产方式在中国企业中也可以采用。实际上,一些日本企业(包括佳能)已经在其中国工厂中实行单元生产方式了。这已经说明单元生产方式并不是非常复杂、中国企业难以学习的技术。单元生产方式下所要求工人具备的技能也不是只有日本工人才具备,中国工人也可以具备。 实际上,单元生产方式固然要求作业者完成比流水线生产方式下复杂的操作,作业者的技能也许高一些,但是这并不意味着操作所要求的技能很高。实际上只要工人在工作中接触到的工作多样一些,接受的培训较多一些,就可以胜任。但是,要培养这些技能,可能需要工人在企业的工作较稳定、时间长一些,对企业流水线上的多个工序的操作比较熟悉。但是在一些以民工为主的企业,人员却欠稳定,尤其是女工们习惯在工作几年后放弃工作、回家结婚,这对她们积累工作所需要的技能不十分有利。但也不是最大的问题。 比工作技能更重要的是,单元生产方式非常需要每一个作业者良好的工作态度。因为在流水线生产方式下,每个作业者的工作态度实际上被不断移动的传送带所控制,作业者的操作速度不能低于传送带的移动速度,否则必然引起积压,并引起现场管理者的注意。因此,在流水线上开小差并不容易。而在单元生产方式,较少的几个人组成生产小组进行作业,又没有传送带“监督”,每个人是否对工作足够投入、富有团队精神就显得很重要。如果一个人工作不负责,其他人可能不一定很容易看出来。所以,佳能集团在进行单元生产方式的革新时,特别改变了人事评定制度。“在人事评定方面,单元生产方式更加看重个人工作态度,能力主义的色彩也更加浓厚”。单元生产是一种独立完成型的生产方式,个人工作态度的评定与过去相比更加容易,为此,长浜佳能对大量超额完成定额的个人和集体设立特殊的奖励。 在调整人事评定的同时,佳能还对教育和训练方面投入了大量的心力,也就是前面提到的“三棱镜式单元生产进修班”。每个投入单元生产的工人在上岗前都要参加专业训练。这种训练也是单元生产方式革新成功的重要原因。 因为单元生产方式是新的、而且更灵活的生产组织方式,对于拆除流水线后单元生产小组如何工作并没有以前流水线生产方式下细致的工作研究所做的作业标准规定,如何工作需要小组的作业者积极地运用技能自己摸索改善工作,正如长浜佳能的“救命女神”生产小组所做的那样。自己摸索改善工作,一方面要求作业者积极努力,另一方面需要工业工程方面的专业技能,这应该也是“三棱镜式单元生产进修班”的培训内容之一吧。但是在日本企业,一贯非常强调现场的改善,强调员工的参与,也很强调对员工的培训,所以关于工业工程方面的基础技能这些员工在平时培训中已经接触并运用,例如参加改善小组活动给公司提改善建议等。 所以,尽管从操作技能上看,中国企业的工人不一定差,但是在工业工程在中国影响很小的情况下,中国企业大多数不了解工业工程,更不用说对工人进行普遍性的培训。缺少工业工程基础知识,尤其是与工作改善相关的知识,应该是中国企业推行单元生产方式时遇到的一个大的阻力。此外,单元生产方式非常强调作业者的团队精神,这一点也是值得担心的。 2003年10月,御手洗冨士夫在大分市召开了一次记者招待会,在会上公布了在大分市修建新的数码照相机、数码摄像机工厂的计划。新工厂占地面积为38万平方米,建筑面积为13000平方米。2004年开始动工,计划在2005年竣工,归属于佳能分公司大分佳能公司。佳能把单反数码照相机等高级照相机的生产放在大分佳能公司,而把低价位的照相机生产放在了马来西亚和中国珠海等地,新工厂的成立将大大增加佳能高级照相机的产量。包括地皮费用,该工厂的总投资约为80亿日元,计划新增员工1500人,在2006年底之前建成产量超过600万台的生产线。在其他企业纷纷向中国转移生产时,佳能的举动给日本产业界带来巨大的冲击。 2003年12月,佳能的成本总额占销售总额的比例是49%,不到50%,横向比较比SONY(67%)、丰田(75%)都低,纵向比较比5年前降低了13%。这是一个了不起的进步,也是佳能“回国生产”的基本保证。 佳能集团等日本企业采用单元生产方式取得成功,也不意味着它们在日本生产比在中国生产更有成本上的竞争力。佳能集团目前在日本生产只是达到了高附加值产品比较有竞争力的水平。明显的例证是,尽管长浜佳能在生产革新上取得了成功,但仍然阻止不了该公司销售额萎缩的趋势,尽管纯利润提高了,但是人员却富余出来了。尽管佳能集团在实行“回国生产”,但是根据御手洗冨士夫的说法,在中国的生产将保持在占佳能全部生产的15%左右。 为了对付中国“人海战术”的竞争,佳能集团要实现“回国生产”,不仅要靠单元生产方式,更要靠活动三维CAD技术设计生产一体化的生产革新、活动佳能独创技术的基本元件、放入“黑箱”中的关键技术等三件武器。 中国企业普遍实行单元生产方式也并不到时候,不仅因为单元生产方式本身的特点,更因为中国企业目前所面临的劳动力供给状况。中国刚刚解决了温饱问题,教育状况虽然有了很大进步,但普遍的教育水平还不高。到工厂工作的工人大部分是来自农村的受教育程度不高的青年,这种情况与亨利·福特在20世纪初面临的情况有很大的相似性。这种情况下,只需要较少技能、只需要较简单的培训就能上岗的流水线生产方式也还具有很大的适用性。在首先解决了企业的用功需要和劳动者的就业需要的情况下,才能进一步试验对流水线生产方式的改善,而流水线的生产效率提高也只能象福特那样,主要依靠专业的工业工程师。 但是,福特的认识有失偏颇的是,即使是从农村出来打工的农民,也并不是只有力气,没有智力,对这些人力资源的看法不应该只使用他们的两双手,还应该逐步使用他们的脑袋,使他们由“片面人”逐步变成“完整人”。这才是符合“科学发展观”要求的有利于最大限度地利用人力资源潜力的可持续的方法。
|