TPS的基本推进方法
▌2-3.自働化 与JUST IN TIME同样重要的是自働化。自働化是以直通率100%为目的而产生的。通过对生产过程中可能出现的各类问题进行归类分析,然后在容易出现质量问题的关键点设上一些工装、 感应器或者防差错设备,各关键点的装置能判断出是否出现异常、出现异常怎么处理。所以运用自働化这种管理思路可以在生产中保证品质。 自働化也有如下原则: 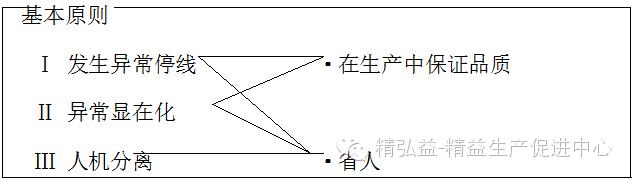
▌2-3-1.基本原则1:在生产中保证品质 《设备的自働化与自动化的区别》 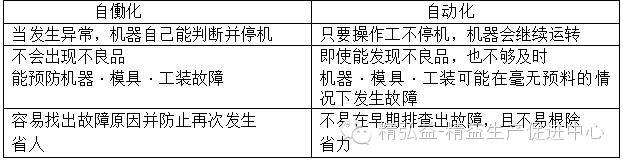
▌2-3-2.基本原则2:省人 从根本上来讲,若当机器运转正常,人不需要在机器旁;操作工只需在机器发生异常停机或换产、交接工作时去查看机器就行了。我们必须将工人和机器要做的工作清楚的分离,让操作工进行没有浪费的作业。 ①在没有做到自働化之前,我们必须在每台设备前都配上一个人,以便随时监控,但若是实现了自働化,工人只需要在工作结束后停机,那他就可以在机器工作期间去干其它的工作,以发挥一个工人的最大效率,以实现省人。 ②对完全自动化的设备,我们一般也会安排工人来监视它的运转情况,以预防问题和保证出现问题的第一时间内解决。但若在生产中设、设置一些可以进行自动监控的装置,那人就可以解放出来了。 从以上意义来讲,自働化将人机分离,可实现省人。 实现自働化的辅助手段参照如下: F P 。。。此种制御装置廉价但可信度高,一旦线体上发生异常,该装置将使生产自动停下,以此防止产生不良品和机器故障(特冰案例) AB 制动 。。。其目的是为了使工位间的半成品的数量一直保持一定。工作原理是按照一定的启动条件,在工序上的两点(A点B点),根据部件的有无来控制的生产。 信号灯箱 。。。它是一种电子显示方式,工作人员一看到这个信息窗口就能知晓现在的生产情况并判断是否有异常。(电子案例)
▌2-4.标准作业
所谓标准作业是以人的活动为中心,将工作按照没有浪费的顺序集中,为了更安全的更有效的生产更好的产品而规定的生产方式。这里需要强调的是:标准作业必须是现场管理者根据自己的意愿亲自制作的,这就体现了“经营现场”的高度,是高业务素质的表现。 作出标准作业的前提条件如下:
▌2-4-1.标准作业的目的 (1)明确生产规则 标准作业是构成生产、管理根基的重要依据,它必须是整体考虑质、量、成本、安全后才确定作业方式。
(2)以此为改善的工具
▌2-4-2.标准作业的三要素 要形成标准作业,这三要素缺一不可 ▌2-4-3.标准作业及改善的步骤 若要对现场作业进行改善,先要将作业现状用图表表示出来,即表准作业。从表准作业中所表示的现象中找出问题点,然后根据问题点的改善来制作标准作业。然后根据这种方式反复对标准作业进行完善。 ① 明确改善的必要性(目标) ② 将现状表示成表准作业(制成表准作业) ③ 以现状为基础,将问题点提出 ④ 改善 ⑤ 制定标准作业 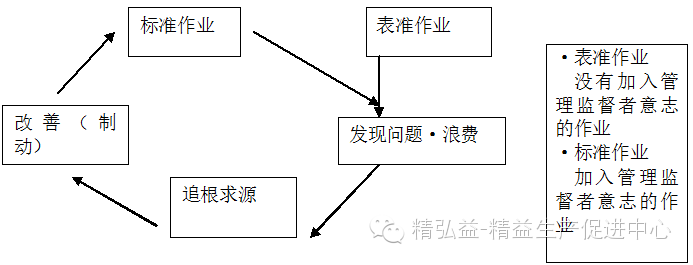
当标准作业被破坏时,一定会发生异常,也就是需要改善的问题点渐渐凸现出来。并且标准作业是相同动作的反复,更容易找出原因并着手改善。
▌2-5.少人化 为了使JUST IN TIME和自働化能高效率工作运转,有一个方法是“少人化”。所谓少人化,是指“根据生产所需要的必要人数,在不影响生产效率的情况下,形成无论用几个人都能进行生产的线体结构”。即:若线体是定时停线,通过将线体无条件减少一个人(一个工位),使线体取得平衡的工作的反复,一直给每个工人安排满负荷的工作。 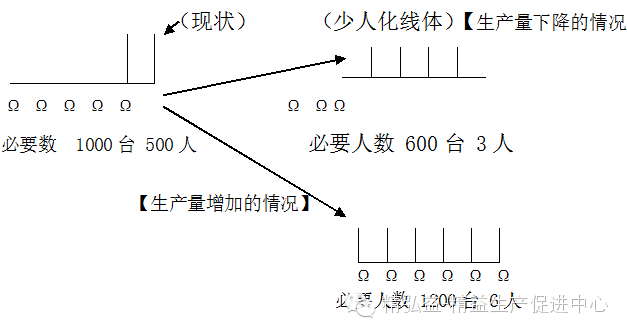
少人化的目标: 可根据台数的变化进行人员的增减 所作的改善效果立竿见影
为了更简单的实现少人化,可从如下方面考虑: ①设计适当的设备,场地布局 ②确保(有)多能工 ③ 定期改订标准作业
推进TPS的基本态度
▌(1) 改善是应需而生的 要弄清真正需要什么 然后根据需要从制定“体系”开始推进 只对有具体需求的部分进行改善
▌(2)对理想的执着追求 ▌(3)现场现物原则 ▌(4)通过“问五遍为什么”来找出问题真正的原因
▌(5)改善不要贪快,与其欲速不达不如慢工出细活 ▌(6)彻底进行设备改善•作业改善
▌(7)必须确保安全和品质
|