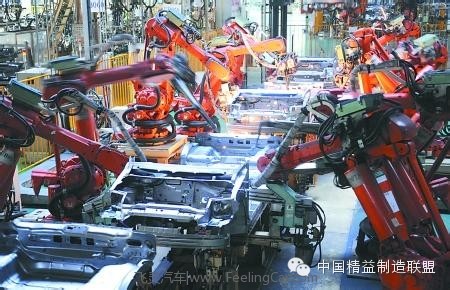
改善!不说我也知道很重要 走进巨大在台中大甲的工厂,生产线上看不到巨大改善前的成堆零件,地上只还隐约可以看见逐渐向生产线移动的限制库存零件摆放的旧油漆痕,象征现场库存不断缩小的历史,这是巨大改善的成果之一。 改善和劝大家做运动一样,说来容易做起来难。“谈到改善真的感觉很无聊,每一次聊到改善,记者不一定会写,读者也不要看。”刘金标说到这里一脸无奈,因为“大家认为你不讲我也知道。” 但是,改善这条路,刘金标带领大家整整走了二十年。
三十年来仍只有一家丰田 2000年,景气开始落入低潮的循环中,台湾的自行车产业面临寒冬。当时自行车市场供过于求、价格下滑、许多协力厂商忙着在大陆布局,台湾自行车产业面临空洞化的危机,身为自行车产业龙头的巨大公司,开始有了忧患意识。
工业局车辆机电组副组长曾繁汉提到,当时自行车产业外移的主要原因就是降低成本,刚好丰田生产方式对成本减低很有帮助,所以工业局和国瑞商量,希望能辅导自行车产业引入丰田生产方式。
在此同时,中卫发展中心研究丰田生产方式也有多年,正好可以从理论咨询方面帮助巨大。当时国瑞汽车总经理原田武彦对自行车产业培训演练并开放现场供他们参观。巨大参加之后下定决心说“这次我们要开始玩真的”。
丰田生产方式不是新招,丰田已经贯彻三十年,市场上介绍丰田生产方式的书籍也多如过江之鲫。“但为什么世界上还是只有一家丰田?”满头银发的刘金标仍然纳闷。
没有做好的原因只有“没有坚持贯彻做理所当然的事”国瑞汽车调达部经理李兆华说明丰田的看法。 听似抽象、平凡且拗口,但这也正是日本丰田汽车在历经石油危机、日本泡沫经济时期,却仍能屡屡创造获利新高的原因。 对巨大也是,丰田生产方式协助巨大摆脱了台湾自行车产业在经济危机之中被连根拔起的灾难。 过去十四年片断的经验,加上开始有老师的真传,巨大才真的打通学习丰田生产方式的任督二脉。 在国瑞协助巨大导入丰田生产方式一年后,巨大的库存从平均7000到9000辆减少到5000辆。今年,在员工人数相同的情况下,自行车产量比三年前增加了20万辆。
丰田的基本精神就是“改善”,要“始于改善,终于改善”,看完书的刘金标体认到,丰田一切都是以改善为出发点,而且永无止境。 但问题是怎么改善,怎么持续? 在改善之前,必须看到问题。丰田强调,“要以白纸的态度,观察生产现场”,所以辅导巨大导入丰田生产方式的国瑞汽车经理李兆华以白纸的态度挑战巨大习以为常之处。不断问“为什么作业员要弯腰?为什么作业员要搬这么重的东西?……”来刺激巨大重新思考设计工作程序。 因为弯腰工作,就代表浪费。于是巨大把这些困难变成题目,想办法解决,就是消除浪费。“过去,巨大总是看得见这些,但从来不认为那是问题,因为习以为常了。”李兆华说。 因此,巨大第一个改变,就是从传统由主管“指挥”作业员的惯性,改为由主管或幕僚单位“服务”于作业员,致力塑造“好的生产环境”给作业员。 现在,巨大所有生产线边,零件、物料都架高,放在作业员垂手可及之处。
从需要出发 丰田的目标是“彻底排除浪费”,而最重要的支柱就是大名鼎鼎的“即时生产(Just In Time),其中最重要的观念就是一切要从需要出发,只能在必要时间,生产必要的量。
产生库存,就是产生浪费。这是从国瑞到巨大,第一个改善的习以为常项目。 改善库存就和清理家里的冰箱一样,只要一次只买一次的量,冰箱里面就会是空的。所以虽然国瑞冰箱总是空的,但要做什么菜都能做得出来,“但很多人冰箱里放的是不想吃的,想吃的冰箱里又没有”。李兆华说。 巨大刚开始的问题也一样。李兆华回忆,“巨大当时要用的零件老是不能到生产线上,但生产线边又堆了一堆用不到的零件” 自主改善的环境 因为过去巨大是制造导向的思考,而非顾客导向。巨大改善调查支援中心郭芳诚经理解释,“以前我们是多生产就代表作业员的效率,到于顾客(后工程)能不能消化,那不是我的问题。” 要落实丰田生产方式要求的“满足顾客需求”,就要力行后工程是前工程的顾客。因为前工程生产的所有零件,一定要是后工程的所需,否则就会造成不必要的库存浪费。 改善库存,达到即时生产的境界,丰田强调必须建构能够让作业员自主管理的环境。其中,在每段工程之间设置像便利商店一样的“店面”,就是一个能够让作业员自主管理、自主改善的环境。 店面就是主管物料的进出。李兆华指出,看店面,就能把握需求与生产的差异。中卫发展中心经理黄肇义分析,“这样可以串起情报流和物流,不会发生要的零件没有,不要的多一堆的问题。 在巨大明亮工厂里,一个制造车架半成品的工程店面里,三篮原本整齐摆放的零件刚被取走一篮,戴着黑色手套、身穿粉红色工作服的妇女作业员开始努力补足被后工程领走的部分。这位妇女作业员同时兼任店面的管理者,随时控制自己做的管件数量是否超出后工程需要的数量。 作业员兼管理者,让作业员愈来愈有责任感。一位在巨大工作十五年的邱姓女作业员,在前年调来担任店面负责人,她原先的感觉是“很累”,因为还要烦恼管理的问题,例如要转换什么车种、进度如何。一年后,管理为她增加成就感,因为求好心切,她竟然清晨四点钟跑到7-Eleven观察怎样补货。 “以前巨大的作业员是矇着眼睛开车,现在店面的设计,让作业员睁着眼睛开车。”郭芳诚形容,因为作业员看清楚前部车的距离,所以会自动加油或踩刹车。 最后,当作业员能睁着眼睛开车,就启动了改善库存的源头。 要睁着眼睛开车,达到持续改善的目标,必须养成习惯。《丰田英二传》一书中提到,“日常理当要做的事情要养成习惯,彻底地实践。”刘金标认为,这同运动的道理相同,刚开始要依靠意志力,然后养成习惯。到最后,“我相信丰田的员工已经上瘾了”。刘金标说。 巨大要和丰田一样,要持续不断地改善,“不能说到什么阶段就可以了,我们要继续推动,你去看,到处都还有浪费。”巨大执行长颜清鑫坚定地说。
看起来,巨大的员工和他们七十岁的董事长刘金标一样,已经上了丰田的瘾了。
巨大的学习——跳脱书的迷思 丰田生产方式对一般人来说很“玄”,容易陷进书的陷阱。正式向丰田拜师学艺,巨大摆脱过去看书学习的迷思。 1、全盘接收吗? 过去从书上获得的情报,很容易陷入只是工具的应用。例如一味地推看板、自动化等,只尝到丰田的手法,但不知真正的目标。 产业特性不同,做法就应该不同。但是精神是一样的,都是要持续的改善,只生产下工程要的。 2、何为零库存?零不良? 零库存,其实还是有库存。只是如何透过改善减半库存,每次1/2库存的N次方改善,慢慢就会趋于零。 零不良,也是有停线,有不良!重点是做到在出现第一件不良品时就把它抓出来。 3、“点的改善”,治标不治本 看到问题,马上解决,这是书的陷阱,使巨大局限于“点的改善”。刘金标始终纳闷,为什么问题已经解决了、改善了,但不久又会旧病复发? 破除改善的迷思就是要“系统化地分析问题”。发现问题,一定要完整地从上游开始分析资料。分析情报如何传递?为何导致物料过多?……
|