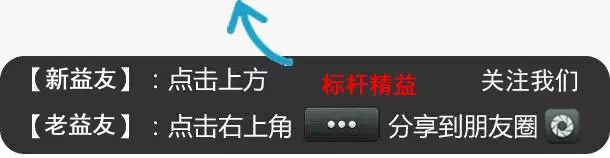
[标杆精益]杂志第427导读
- 如何在企业中推行OEE
- 选拔人时要从最优秀的人开始
- 何解所有的进步都依赖于不讲道理的人?
- 工业4.0落地巡礼:海尔沈阳数字化互联工厂
- 揭秘苹果Mac Pro精益生产过程 这才叫生产线!
新益友请关注“标杆精益”,点击“查看历史消息”查看全部文章。
‍‍
如何在企业中推行OEE (益友原创文章)
一、推行OEE的前提与目的 在讲解推行OEE之前,首先要明确推行OEE的前提(局限性)与目的(益处)。
前提条件: 目的(益处): 降低生产停机导致的产能损失 减少设备的维修费用 提高生产能力,增加产出 降低产品质量问题
看到上面的目的(益处),也许就很想在公司内推行OEE了,但是OEE仅仅是一种可选择的统计工具,而不是必须的工具,如果有些企业或者工程师有其他能够达到上述目的的工具,也是可以所使用的。同时,OEE计算是为了找出影响生产效率的主要因素,针对主要问题采取相应的对策,并确定负责人进行引导与相关辅助人员进行改善。
二、OEE的概念 OEE是英文OverallEquipment Effectiveness的缩写,中文是设备整体利用效率,设备综合效率,生产系统综合效率,是一种透过六大损失,寻找影响生产效率的根本原因,并提出相应的长短期解决措施。 具体的计算方法,在后面进行讲解。
三、六大损失 提到OEE,必须要知道影响我们OEE指标的6大损失,以便更好的进行分类汇总,确定相关负责人。
6大损失主要为以下损失: A.设备故障损耗 B.换型转产、安装调试损耗 C.空载、短停损耗 D.速度低下损耗 E.预热(启动)损耗 F.不良、返工损耗 G.其他损耗
下面将详细的讲解各大损失主要出现的情况(如有疏漏,欢迎阅读者联系我,感谢)
B.换型转产、安装调试损耗
换型的工时损失,换型后的设备调试 刀具、备件定数寿命更换 工艺变更,设备参数的调整
C.空载、短停损耗(一般指5min以下不需要维修人员协助的情况下)
D.速度低下损耗 进给率、调整率不再100% 设备皮带等相关辅件导致的速度低下
E.预热(启动)损耗 冬天机器热机、液体升温 过度预热的时间损失
F.不良、返工损耗 来料加工后发现的原材料不良 制程导致的报废(参数调整、崩刀等)
G.其他损耗
停工待料 产线等待人员 等待首件报告进行确认开始生产 员工对设备进行重复调整的损耗 不熟练员工对设备操作的工时损耗 物流不顺畅导致的损耗
四、计划停机 上述6大损失和其他损失是影响设备的负荷时间的,下面就是不包含在负荷时间内而在整体的使用时间(日历时间)内而对设备造成计划停机因素:
五、如何计算OEE 1. 复杂的计算方法
OEE=时间利用率*性能利用率*良品率 时间利用率=(负荷时间-停机时间)/负荷时间 (A.B.E) 性能利用率=速度运转率*有效运转率 (C.D.G) 速度运转率=基准循环时间/实际循环时间 有效运转率=(产量*实际循环时间)/(负荷时间-停止时间)
良品率=(加工数量-不合格品数量)/加工数量 (F )
2. 简单计算方法 OEE=(合格品数量*基准循环时间)/负荷时间 其实通过上述公式的化简,最终就是简单计算方法公式
六、推行OEE的措施 通过上述基本概念、计算方法、影响OEE的6大损失,下面就开始讲解如何在工厂内推广OEE,如何更好地实施OEE。
相关部门培训,概念引入 在推行OEE时,需要对生产部门主管、设备维修人员、制程工程师、质量工程师进行概念培训,重视OEE的指标,并积极配合落实相关问题点的改善实施。
生产现场的生产看板 生产现场制定相应的生产管理看板,生产作业员、班组长、主管、经理等使用不同颜色的笔在看板上进行书写与标记。 生产看板包含以下内容:(各公司生产看板不同,依据公司实际情况而定)
1-8小时 理论产出 实际合格品产出 Down机类型 Down机时间 其他(长短期策略、负责人、OEE 目标)
每日生产报表的反馈与问题统计 生产主管需要将每天的生产报表进行统计,或者发送给对应区域的IE进行统计分析,统计出每天的OEE情况,以及导致OEE低的相关原因。 制作柏拉图,发现主要原因。 现场区域生产早会 生产现场的早会需要生产主管、IE、ME、QE、维修等人员进行参加,针对昨天三班出现OEE低下的基本原因,生产现场的早会需要提出,并在早会上确定相关的责任人和结束日期,并书写在生产看板上。 OEE的计算与问题分类 针对每天的OEE与相关问题统计,IE或者生产将出现的问题进行分类汇总,并填写每日的OEE报告,统计到每周。在下周一统计完成将其发送给区域的生产主管,并由其填写另一张对应问题解决措施表格,统计出每周出现的问题和责任人与结束日期。 每周OEE会议 每周一召开上周的OEE会议,需要生产主管、IE、ME、QE、维修全程参与,可由IE进行组织协调,以生产部为主导。 会议内容主要为: 上周OEE的基本情况,上是否达标 查看区域影响OEE原因的柏拉图 针对柏拉图上的TOP3 原因进行分析并找出根本原因 如果早会上某些原因未能提及或者未能确定责任人,须在OEE会议上确定 回顾至目前为止,相关问题还未关闭,进行跟踪,更新日期等 相关措施进度通知 如果问题负责人有问题的相关进度与相关需求,需邮件通知相应人员进行协助,或者告知目前的问题进度。
七、OEE实例分析 复杂计算: 时间利用率= 320/400 =80% 性能利用率= 0.01*20400/320=63.75% 良品率 = 19600/20400=96.078% OEE = 80%*63.75%*98%=49% 简便计算: OEE= 19600*0.01/400 = 49% 具体通过上述发现,影响设备效率的主要是大量的短停和空转、速度的损失,针对上述问题进行确认相关负责人并进行改善.
=========== 作者授权《标杆精益》发布,转载请附上以下全部内容,违者心究。 =========== 作者介绍:
Jackson Cao/曹军胜
益友会苏锡常分会副会长
益友会安徽分会副会长
欢迎与作者交流:
QQ: 513305625 E-mail:ie.jason.cao@gmail.com
|