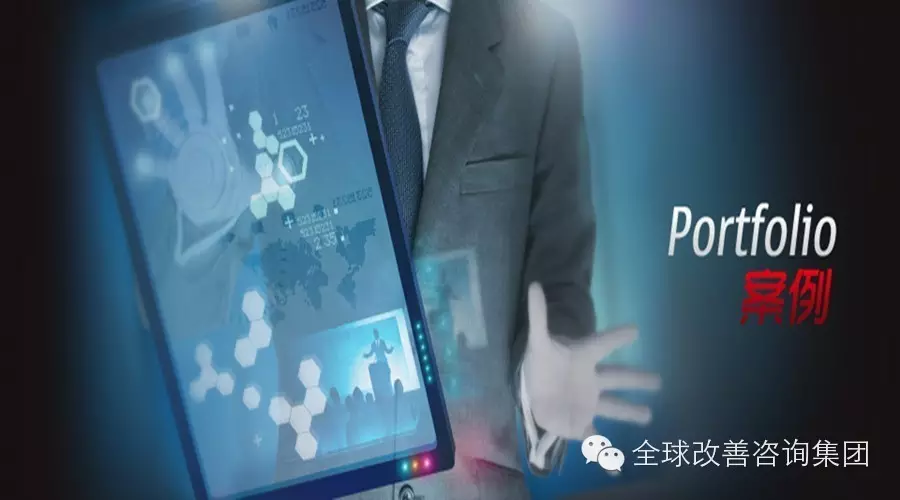
随着市场需求的日益增加,为满足交货需求,本年度生产产能需提升30%,通过梳理现状,发现车间现场混乱、物流资源耗费大、工序间交叉多、员工走动搬运多,现有的布局限制了生产效率的提升,达不到精益中“流动”的要求,布局成为达成产能提升目标的绊脚石,车间布局改善势在必行。 项目目标: 产能提升30%,在制品库存周转天数降低30%,制造周期缩短10%,车间产品移动距离降低50%; 布局改善方案确定: 工艺、技术、设备、生产等部门人员组成项目团队对现状进行梳理: 一、现场问题查找 ⑴工位线材存放过多且放置混乱,寻找困难,长期存放对产品质量有严重影响; ⑵模具运送距离过远; ⑶物料通道窄,不方便原材料运送; ⑷线圈绕制完工后,频繁使用行车吊运。 团队分成四个小组,根据3P布局思路,结合平面沙盘,针对生产现场问题现状、厂房面积、人员与设备能力,各团队讨论并产出两套改善方案,最终形成八套方案。综合每套方案的优点及公司领导期望,形成布局改善的最终方案。 现场模拟: 确认最终的布局方案后,进入到现场模拟改进阶段,以作业平衡,减少现场浪费为准则,通过实地测量、模拟实验制定出工装设计方案以及设备拆迁计划。 布局的调整有以下几个亮点: 1.将空心绕线机设备调头,预留出足够的物流运输通道,确保生产过程安全,同时缩短了线圈的运输距离。 2.将绕线和套装进行单元化生产,减少线圈绕制完工后使用行车吊运到套装工位的距离,减少生产占地面积。 3.建立完整的物料运输和人员通道,实现物流运输和人员通道分离,物流通道的运输实现由东向西一致化建设。 局部优化: 布局调整之后我们在生产过程中依旧发现各个工序内部布局存在不合理现象,局部物流不顺畅,因此各班组开始展开局部优化。 1. 空心绕线区添加液压升高台,减少员工上下攀登的次数,避免安全事故的发生。 2.针对铁心横剪区经过横剪机的硅钢片放置问题,制作实用于现场的运输工装,避免搬运浪费和划伤的危险。 通过全体员工的努力,整个过程共完成自主改善200余条,改进工装70余件。 项目成果: 最终电抗器车间产能提升34%,在制品的库存周转天数减低30%;制造周期缩短11%,车间产品移动距离降低65%;,成效显著。 现场管理能力得到提升,创造了一个轻松舒适的工作环境,员工积极参与改善,精益文化融入每一个员工的内心。 作者:某变压器公司余进洋、张高伟
|