普通公司的习惯→库存是“资产” vs Toyota 的非常识习惯→在库是“罪库”
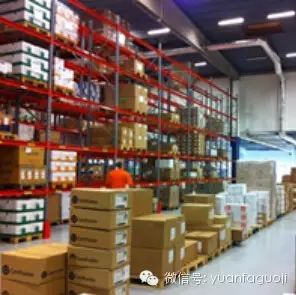
丰田式为什么要严守“必要的东西在必要的时间只生产必要的量”,是因为这是盈利第一要则。 丰田式中,即便机器有一千个的生产能力,如果预估销售量有六百个,就只会在怎么便宜地生产这六百个上面下功夫。但是,一般企业有一千个的生产能力就会集中生产一千个。然后再想办法怎么卖掉这卖不出去的四百个。这就是库存。 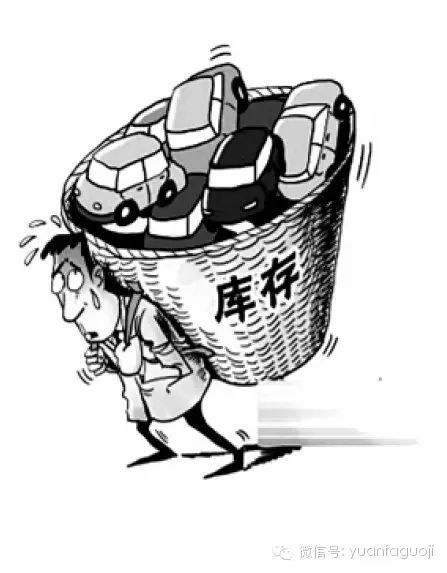
但是,库存什么时候能卖出去是不知道的。卖剩下的情况很多。有时候还要清仓大甩卖。但是,库存是已经花费了材料费、人力费、能源费的。
也就是说,库存是占用了多余金钱的“罪库”,这样想更符合现实。 即便是这样,一般企业还是会认为“集中生产更便宜”“设备如果不满负荷运转的话折旧费用负担会变更重”“库存也是‘资产’,所以账面上不会亏损”,觉得“在库是罪库”这样的说法很难理解。 要实践丰田式成本削减,就必须要统一以库存为首的“什么是浪费?”的思考方式。生产过多是最需要警戒的事,如果不能以此为常识,就很难实践丰田方式。 首先,丰田式导入的最初,要统一“什么是浪费”。有的人觉得是“浪费”,别人觉得“不是浪费”的话,构成丰田式改善核心的“消除浪费”就无法进行下去了。 丰田式中的所谓浪费,就是指附加价值无法增加的现象、结果。 在生产现场,动作分为“作业”与“浪费”,作业又分为“附带作业”和“增值作业”。也就是说,分为“浪费”“附带作业”“增值作业”这三种。 “浪费”就是作业中所不需要的、只会提高成本的动作。需要立刻避免。 “附带作业”是不带附加价值的作业。本身是浪费,但是大多数情况不得不去做。为了避免,需要改善作业条件。 只有“增值作业”是会提高附加价值的真正作业,是可以称之为工作的。 以这样的视点来看生产现场,就会发现以下八种代表性浪费。 ① 不良、修理的浪费······生产了不良品、手修品,使品质降低、成本增加。
② 生产过多的浪费······丰田式中最需要警戒的浪费。
③ 加工本身的浪费······与工程的推进方法、精度无关的不需要的加工等。
④ 搬运的浪费······追求Just in time (必要的东西在必要的时间只生产必要的量)所需要的搬运以外的的搬运行为。
⑤ 库存的浪费······纳入的部品、各工程间的半成品的持有量超过需要的量
⑥ 动作的浪费······不产生价值的人的动作、机器设备的动作。
⑦ 等待的浪费······只是在看守设备、机器在加工过程中不用出手作业的状态等。
⑧ 产业废弃物的浪费······材料、包材、一次性容器等的废弃浪费。
Toyota的非常识习惯→ 公司内要统一“什么是浪费”。
|