在工厂内以何种方式来安排各部门的布局,受到工作流形式的限制。按工作流程形式分类,可以分为三种基本类型(工艺原则布置、产品原则布置、定位布置)和一种混合类型(成组技术布置)。 1 工艺原则布置(process layout)。 又称机群布置或功能布置,是一种将相似设备或功能集中布置在一个地方的布置形式,比如按车床组、磨床组等分区。被加工的零件根据预先设定好的流程顺序,从一个地方转移到另一个地方,每项操作都由适宜的机器完成。它通用于多品种、小批量生产方式。 医院是采用工艺原则布置的典型。 工艺原则布置是最常用的方法,用于对具有类似工艺流程的工作部门进行布置,使其相对位置达到最优。在很多设备安排中,最优布置通常意味着妥善安置相互有大量运输的内部,使总的物流运输管理费用最小。其优缺点如下: 优点 | | 1.机器利用率高,可减少设备数量 2.可采用调用设备
3.设备和人员的柔性程度高,便于更改4.产品品种和数量
5.设备投资相对较少
6.操作人员作业多样化,可提高人的工作兴趣和职业满足感 | 1.由于流程较长,搬运路线不够合理,运费高
2.生产计划与控制较复杂
3.生产周期长
4.库存量相对较大
5.由于操作人员从事多种作业,需要较高的技术等级 |
2 产品原则布置(production layout) 也称装配线布置,是一种根据产品制造的步骤安排设备或工作过程的方式。产品流程是一条从原材料投入到成品完工为止的连续线。固定制造某种部件或某种产品的封闭车间,其设备、人员按加工或装配的工艺过程/工序布置,形成一定的生产线,适用于少品种、大批量生产方式。 产品原则布置与工艺原则布置之间明显不同的特性是工件流程模式。在工艺原则布置中,物流线路可变性强;而在产品原则布置中,设备和车间服务于专门的产品线。所以,在一个产品原则布置系统内,各部门的相对为止以及生产部门内各部分定位所出现的困难比工艺原则布置要小。其优缺点如下: 优点 | | 1.由于布置符合工艺过程,物流顺畅
2.由于上下国内供需衔接,存放量少
3.生产周期短
4.物料搬运工作量少
5.可做到作业专业化,对工人的技能要求不高,易于培训
6.生产计划简单,易于控制
7.可使用专用设备和机械化、自动化搬运方法 | 1.设备发生故障时将引起整个生产线中断
2.产品设计变化将引起布置的重大调整
3.生产线速度取决于最慢的机器(TOC)
4.相对投资较大,因为在生产线上有的机器负荷不满
5.生产线上重复作业,易使工人感到单调乏味,产生厌倦
6.维修和保养费用高 |
3 定位布置(fixed layout) 产品(由于体积或重量庞大)停留在一个位置上,设备、人员、材料都围绕产品而转。 飞机制造厂、造船厂、建筑工地等都是这种布置方式的实例。 与工艺原则布置和产品原则布置相比,定位布置的特点是具有相对较少的产品数量。在定位布置中,按照作业的级别安排顺序相当普遍。根据先工序决定生产阶段,应按照物料技术优先性安排物料。其优缺点如下: 优点 | | 1.物料移动少
2.当采用班组方式时,可提高作业连续性
3.提高质量,因为班组可以完成全部作业
4.高度柔性,可适应产品和产量的变化 | 1.人员和设备的移动增加
2.设备需要重复配备
3.工人徐亚较高的技能
4.会增加面积和工序间存储
5.生产计划需要加强控制和协调 |
4 成组技术布置(group layout) 成组技术布置是将不同的机器组成加工中心(工作单元),对形状和工相似的零件进行加工。成组技术布置和工艺原则布置的相似店是都有特定工艺过程。加工中心完成的品种有效,适应于中小批量生产。 成组技术布置目前被广泛应用于金属加工、计算机芯片制造和装配作业。成组技术布置可以通过以下三个步骤实现:一是将零件匪类,二是识别零件组的物流类型,三是将机器和工艺分组,组成工作单元。其优缺点如下: 优点 | | 1.由于产品成组,设备利用率较高
2.流程通顺,运输距离较短,搬运量少
3.有利于发挥班组合作精神
4.有利于扩大工人的作业技能
5.缩短生产准备时间
6.兼有产品原则布置和工艺原则布置的优点 | 1.需要较高的生产控制水平以平衡各单元2.之间的生产流程
3.如果单元之间流程不平衡,需要中间存储,增加了单元之间的物料搬运
4.班组成员需要掌握所有作业技能
5.减少使用专用设备的机会
6.兼有产品原则布置和工艺原则布置的缺点 |
系统布置设计 对于某些类型的设施布置问题,车间之间的流量实际上不可能得到,有时不易提示的定性因素却对布置决策起着决定性作用,此时可以用一种经典方法――系统布置设计(system layout planning,SLP)。 系统布置设计是在1961年由缪瑟提出,是一种条理性强。将物流分析与作业单位关系密切程度分析相结合求的合理布置的技术。 SLP采用四个阶段进行,如下图所示
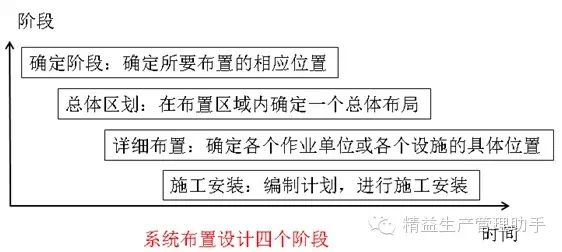
SLP设计流程如下: 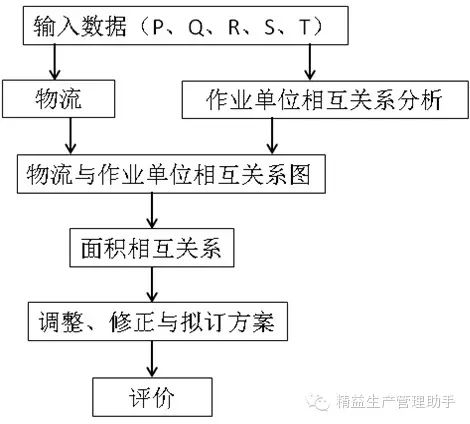
|