精益生产、精益管理是一种经营管理理念,强调持续改善,全员参与,它不特指某一种方法或窍门,而是企业走向卓越的一个持续不断的改良过程和行动。 通过减少生产、管理中的设备、人员、原料、库存浪费来降低成本,通过优化工作流程来提高生产效率,做到高品质、准时生产、敏捷交货,是企业学习精益制造的目标之一。但是在实践中,不少企业认为所谓的精益制造就是5S、看板管理、TPM等一系列工具,因此,流于形式的学习模仿导致事与愿违就不足为奇了。 改善重在持续是开展精益生产、精益管理的态度。某石油钻头公司(以下简称“A企业”)副总裁在总结公司十多年跟踪学习精益制造模式的经验时说:“精益生产的优化是整体系统的优化,而非局部系统的优化。作为本土化的公司在导入精益生产经验时,应当做好长期坚持的思想准备。”
从1994年介绍丰田汽车精益生产模式的《改变世界的机器》中文版面世开始,该企业就接触并学习精益生产的相关概念和做法,重新布置生产线,改变过去按工艺流程布置设备的做法,把几十道工序集成到多功能的机床上。过去十台设备生产一个品种,生产改造之后,十台设备就是十条生产线,产品生产周期也缩短了,原来生产一批钻头要三四个月,之后缩短到了八周,产量也从过去一年生产一万多支增加到四万多支。 从1994年到2004年的十年间,A企业主要是在生产组织和设备管理上做工作,主要还是生产现场的改善。“当时,精益生产的氛围不算浓,领导强调的多就做得多一些,有时推行两三年后再看,情况又倒回去了。”A企业的管理层认为虽然引入精益生产比较早,但最初的十年并没有从全局的角度把这种模式渗透下去,“因为属于从上往下推动的生产改造,所以没有形成持久的生产模式。” 所幸的是A企业管理层一直把精益生产当作制造业发展的方向,虽然没有形成体系,但始终在推动精益生产上做探索和努力。2004年,A企业引入了一些具象化的管理活动:5S管理、改善提案、改善课题、阶段性改善等,在做到一定的程度后又导入标准化、TP自主管理、价值流分析等工具。“我们把改善全部融入到管理活动当中去,以前A公司也曾搞过所谓的‘提合理化建议’活动,但那是给别人提意见,而改善提案和改善课题是工人围绕各自的岗位提改善建议,并去实施。因为有了这些管理工具做载体和平台,一步步地带着我们往前走,做的就跟原来虎头蛇尾的状况不一样了。我们强调‘事事都有改善的空间,人人都有改善的能力’。”A公司某高层如是说。 找准切入点,全民参与改善与A企业最初自上而下推行精益生产有所不同,生产办公及生活家居的B公司认为发动一线员工自发改善的热情是开展精益制造的关键。因此,B公司首先解决的是让员工愿意做改善的事情,从“要我干”变成“我要干”。 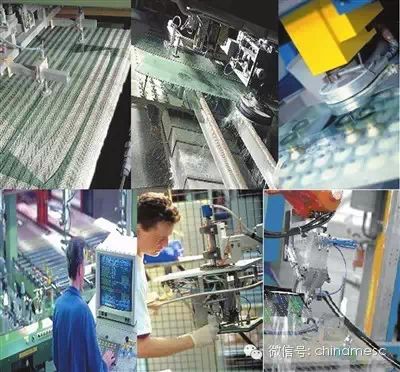
如何引导员工对现场改善、流程优化这些“跟自己看似无关”的事情关注并投入热情呢?B公司副总裁说:“我们的切入点是降低粉尘,在降低劳动强度的前提下提高生产效率。” 家具行业有个特殊性,就是粉尘比较大,开料打磨都会产生大量的粉尘,工人们工作两个小时头发都会变白。为此,B公司组织工人、设备技术人员,以及专家在一起考察粉尘主要来自哪些环节,如何回收粉尘。因为现场的整洁带给员工的是舒适,因此工人提改善提案的热情很高。通过一些小的设备改造,4个多月下来,车间的粉尘问题基本解决;工人的改善意识也大幅提高,有好几百个提案都得到了实施。 “工人以前觉得干活脏是正常的,其实他们都是能工巧匠,最了解现场和工作流程中的一些问题,只要他们感兴趣,关注了这些问题,解决方案自然就出来了。”B公司副总裁说,“要提高产量,一种方法是让工人变得更累,另一种方法是让他轻松的同时提高生产率。” 通过流程和设备的改善,B公司将过去对生产没有价值的流程剔除掉,比如对于工人来说定螺丝是必要的,但是拿螺丝的动作和过程是没有价值的,那就通过工具的摆放来简化整个工作流程,这样工人完成工作既快又不像原来那么累。“走路、弯腰其实浪费体力,我们就是通过减少这种消耗来提升人均每小时的劳动价值,这样产品产量提高了,劳动强度却下降了,是两全之策。”B公司生产经理说。 B公司从降低粉尘入手开展精益生产是结合自身行业和企业特点做出的选择。这一点对于想引入精益管理的企业来说很重要,“很多企业一上来就学丰田,搞看板,结果失败了,原因就是没有基础。精益生产要根据每个企业的实际情况来选择切入点和改造重点。” 循序渐进,逐层深入精益生产和精益管理是个循序渐进的过程,不能一撮而就。以上两个公司都是从改善提案做起,先改善一个工序、环节的问题,再进入涉及多环节或者多部门的流程优化。改善课题通常由部门、车间或跨部门的负责人组成一个团队来解决,“把问题抛出来,根据调查数据,立项写计划,然后实施,检查确认效果如何,最后将有效的流程标准化。这就是所谓的PDCA(Plan-Do-Check-Action)”A公司某高层介绍说。在A公司,改善课题分为A级和B级,A级属于公司级的,有专门的精益管理部门进行监督和指导;B级的课题就由相关部门自行负责实施,公司只定负责期检查。 通过流程改善,B公司制作沙发的周期从原来的7天缩短到了一天半。他们改变了家具行业分散式作业的工作方式,形成标准化的流水线,从而做到了批量化地制作家具。 从原来的现场改善,到流程优化,再到如今正在逐步地将精益管理引入研发领域,称为并行开发。也就是从产品立项开始,研发、销售、采购、市场就必须参加,“过去研发自己闷头干,研发、生产、销售环节是一个环节接一个环节,‘串联式’的,现在我们把他们几个部门组织到一起,共同参与产品定位、价格、市场策略的制定,并明确各自的任务”,这样产品从立项开始,其他部门就着手各自的工作,不仅缩短了彼此沟通的时间,而且也有效预防了出现问题互相扯皮的现象。并行工程实施后,B公司新产品的销量与原先比增长了七八倍。 奖励考核制度是保障A公司五年前将精益管理奖提到总公司层面。每个季度子公司对申报的改善项目进行评级和奖励,虽然钱不多,但是通过公示、组织发布会等形式,为优秀员工提供一个展示自己成绩的舞台。每半年总公司都会举办改善项目发布会,全体领导都参加,气氛隆重,营造重视改善的企业氛围。另外,在奖励机制上对于改善项目允许重复激励。比如原来工会有技术革新奖,团委也有创新奖,这样有可能一项提案能够同时得到几个奖励,虽然钱不是很多,但是重在荣誉,使得员工的积极性很高。 在考核方面,A公司也将精益管理纳入其中,为了使考核更能体现员工工作效率,将考核授权全部下放到基层,主管直接负责员工的绩效考评。 管理者角色的转变企业开展精益管理成功与否的首要前提是高层领导的重视和支持。领导有没有决心做这个事很关键,出现问题,不能轻易怪下面执行不好,执行不好还是上面有问题:在资源上是否做到及时响应和支持;定目标的时候是不是好高骛远等。 由于精益管理提倡的是全员参与的持续改善,所以对于企业中层以上的管理者来说,如何激发员工的改善热情也成为工作的重要内容,相应地对于管理者的评价标准也会有所改变。管理者要从医生和警察的角色扮演转变为教练,教练的职责就是看到问题点,启发员工如何做的更好,让他自己去实践。
|