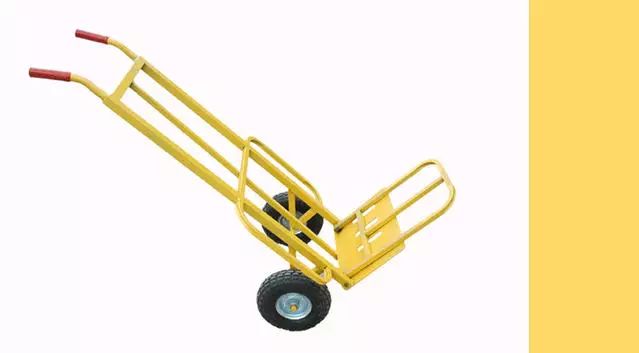
往往精益人在推动企业精益生产活动时,直接从5S浪费开始,全员开始进行消除浪费的活动,忽视基础IE的手法和理念的应用,在消除浪费时,精益告诉你什么是浪费,除了ECRS/5W1H,其他消除的方法呢?
如果在基础IE中,消除的方法就会很多,线平衡、动作分析、操作分析、程序分析等等,同时还能做到标准化,我们上周提到的整体效率分析(回复4009可查看)中发现的很多问题,完全可以利用基础IE手法有的放矢的去处理,并且很有说服力。
IE作为精益的基础有着自己的特点,推行精益就是要夯实基础IE;所以不得不说的就是IE的学科特性:
(1)IE的核心是降低成本、提高产品质量和生产效率,追求生产系统的最佳整体效益。
(2)IE是综合性的应用知识体系,它是把技术与管理有机地结合起来的综合学科。
(3)以人为本是IE区别于管理工程学科的特点之一。
生产系统的各种组成要素中,人是最活跃和最不确定的因素;IE为实现其目标,在进行系统设计、实施、控制和改善的过程中,都必须充分考虑人和生产要素之间的关系和相互作用,以人为中心进行设计。
从操作方式、工作站设计、岗位和职务设计直到整个系统的组织设计,IE都十分重视研究人的因素,包括组织关系、环境对人的影响以及人的工作主动性、积极性、创造性及激励方法等,寻求合理配置人和系统,建立适合人的生理和心理特点的机器、环境和组织系统,使人能够充分发挥能动作用,从而在生产过程中提高效率,安全、健康、舒适地工作,实现个人及组织价值,进而更好地发挥各生产要素的作用。
(4)IE的重点是面向微观管理。
从制定作业标准和劳动定额、现场管理优化直至各职能部门之间的协调和管理改善,都需要IE发挥作用。
(5)IE是系统优化技术。
IE所强调的优化是系统整体的优化,不单是某个生产要素(人、物料、设备等)或某个局部(工序、生产线、车间等)的优化,最终追求的目标是系统整体效益最佳。所以IE从提高系统总体生产率的目标出发,对各种生产资源和环节具体研究、统筹分析、合理配置;对各种方案作量化的分析比较,寻求最佳的设计和改善方案,这样才能发挥各要素和各子系统的功能,协调有效地运行。
日本在推行精益生产时,运用了基础IE中大量的作业研究、动作研究、时间分析技术,使精益生产始终站在科学的基础上,因此生机勃勃、卓有成效。
日本企业在运用IE方面有极大的创造,使得精益生产不仅带来了生产组织方式的质变,而且带来了产品开发、质量控制、内外协作管理、与用户关系等一连串根本性的企业组织体制、管理体制方面的重大变化和企业经营价值观的重大改变,其中最受影响的还包括日本企业的企业文化。
只有通过找问题、提问题、改善操作、优化管理,最终对形成产品质量的所有工序、环节、作业都作了改进,在这个基础上制订的标准,才是高质量的、可操作的、有群众基础的;有针对性地开展IE,推进精益生产,实现物流、作业的优化,才能向精益生产靠拢。具体讲就是组织以降低库存为目标的准时化生产和以优化作业、提高劳动效率为目标的作业分析。
在推进精益生产的过程中,运用IE工序分析方法通过对整个制造过程的分析、产品材料的流程分析、多人作业程序分析和布置与线路分析,实现生产作业系统的优化,才能为精益生产的深入推进打下坚实的基础。
|