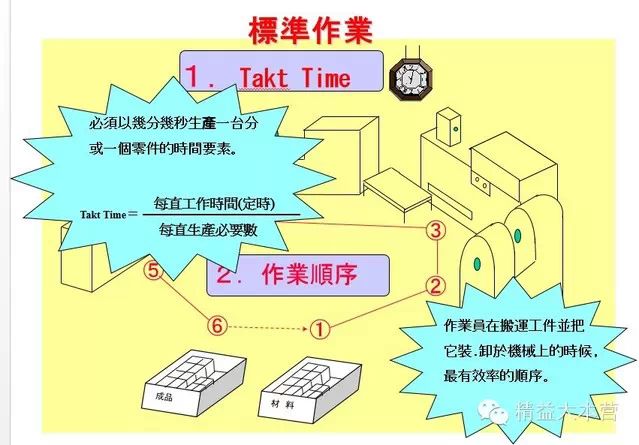
点击标题下面蓝色字体“精益大本营”地方即可关注我们精益平台,订阅后,点击"查看历史消息”查看精益全章! 3、标准作业和作业改善 (1)作业改善基准介绍 有些工厂,说是进行改善,但不是进行复杂的作业系统改善,而是进行设备升级改善。改善本来是为了降低成本,却花费大量的金钱购进新设备,导入新设备后形成新的瓶颈和产能不平衡的问题,当事人觉得已经进行改善了。无论怎样讲使用什么样的设备,应该按照产能平衡和订单特点来决定,由设备规格来确定如何生产布局和作业设计的做法,完全是本末倒置,这种现象在工业历史较短的国家和企业比比皆是,甚至说如果没有了中国人买昂贵的设备充面子,日本和德国的设备厂都得倒闭的现象,日本在1993~2003十年经济停顿中,正是中国经济发展中盲目购进先进设备的现象才使他们度过难关,这不论在投资上还是在管理上都是极大的错误。 作业改善包含如下项目。 ① 首先物流结构的改善 改善物流结构,大致上可以分为两种情况。一种是将相互远离配置的机械设备按照工程顺序相互接近摆放在一起,这种方法叫流动车间型的“配置改善”。 另一种是,终止物品大批量的流动方式,而以小批量或单个的方式向下流动。这种办法叫“流动单位的改善”。 ② 作业合并的改善 以前将作业细化,然后确定作业岗位,通过手工传递或传送带传送物品。在这种情况下会发生将工件拿起和放置的浪费,平衡浪费也极其严重。在一个流改善中刚好相反,要改为步行动作最小,由一个作业者一直做出成品的“多工序合并”的改善。 ③ 作业动作的改善 将步行、手腕移动等动作上的浪费现象去除。在此,可以将IE中的动作分析作为基础。另外,机械设备布局不良、零件放置位置不好等也和人的动作相关,导致动作浪费。要想去除动作浪费,需要对设备布局、零件的放置场所、放置方法等进行改变。 ④ 将作业规则化 如果每次作业的时候,其作业方法或内容都发生变化,那么,该作业将不容易被所有的人掌握。因此,需要将作业规则化,使不论是谁都可以用相同的方式进行作业,并且,谋求标准化是这里的关键。 以这些作业改善为基准,为了和作业改善相适应,需要对设备进行改善,思路如下所述: ⅰ使设备符合作业的改善 对用于大批量的设备、大型的设备、高速设备等进行改造,使其和改善之后的作业相匹配。在大多数场合,速度平缓的专用设备更容易保证质量,并且,体积小的小型设备才容易嵌入到生产线中。 ⅱ使用人和机器可以分离的离人化机器 即使合上开关,也必须由人来推动工件的设备,对机器进行改造,使人可以不用跟随着机器。这种情况就被称为“离人化”。是使人和机器分别产生附加价值的改善方式。 ⅲ进行改善,使机器不会造出不良 在生产过程中,当要出现不良时机器就能停下来,并通知人进行判断。使其具有哪怕是一个不良也不制造的设备。 如前所述,改善活动既有作业改善又有设备改善,但绝对要保证首先进行作业改善。另外,在作业改善中,将动作浪费去除非常重要,但最重要的是作业的“结构改善”。结构改善将改变流动的单位及迄今为止的设备布局。 (2)物品流动结构的改善 在作业改善中,最重要的改善项目是将“物品的流动结构”改变。这种改变结构的含义是,将迄今为止的作业方法在根本上加以否定。如果不进行意识改革,就不能发生真正的改变。 因此,所谓将物品的流动结构改变,换而言之,就是要将头脑中的思想切换,改变对机械设备的思考方法、改变设备布局、改变物品的流动单位。其要点是,将物品制造中的所有事项加以改变。 图5-3是一个半导体晶片焊锡印刷工程中物品流动结构改善的例子。 改善前,该工程配备了4名作业者,采用各自独立的作业方式。采用以600个为单位的批量制造方式,使用大型干燥机,在投入、取出时,工件非常混乱,这样的非智能设备成了生产的瓶颈。 于是,将①印刷(表)、②烘焙、③印刷(里)、④回流焊投入、⑤回流焊取出工程由一人完成,变为“多工程持有”,这样,动作浪费最少,然后进行“布局变更”,使设备布局更易于作业,并且采用了和回流焊夹具相匹配的“两片流动”。此外,终止使用大型干燥设备,将仓库里闲置的小型紫外线干燥机进行改造,使其“生产线嵌入化”,给回流焊炉增加将工件送回的传送带,使投入(I)取出(O)合一,形成I/O一致。通过这些改善,实现了少人化,人员只要2名,生产效率也增加了一倍。 (3)作业动作的改善 作业者作业的全部内容,是不是都能产生附加价值呢?答案是否定的。并且,大部分是不会产生任何价值的单纯的动作。将这些单纯的动作去除,使工作变的更有效率,这就是作业动作的改善,也称为动作研究(Motion study)。 所谓动作研究,就是将作业中的无用动作去除,更加容易地将动作的方法及顺序等进行组合,并且将其标准化。 “动作经济的原则”在动作的改善中非常有效,通过将无用、不完全、不合理的等等应付了事现象去除,使作业动作变的更加经济。因此,不但需要对人的动作进行改善,还要对与此相关的放置方法、夹具、作业环境等等进行改善。 ① 零件位置的改善 图5-4是一个对捆包用塑料袋进行改善的例子。改善之前,捆包用塑料袋放在作业者的后面,改善后,将塑料袋吊在作业者的前上方,这样,作业者一步也不用走,就可以一个一个地取下塑料袋了。 ② 零件取出的改善 图5-5是装配作业中零件取出改善的一个例子。改善之前作业台很大,作业者离零件的距离很远,并且,零件的放置方式为平放,导致零件拾取困难。 改善之后,将作业台缩小到最小限度,作业者和零件间的距离拉近了,同时,零件的放置方法为倾斜放置,拾取容易。
③ 由单手作业向双手作业改善 图5-6是一个将电话按键(推挽式按键)装配作业的单手作业改为双手作业的例子。 改善前,没有将工件固定的夹具,使用左手按住工件,右手将按键一个一个地插进去。 改善后,制作了可以使用左手的夹具,使双手能同时插入按键。另外,为了防止将按键装配错误,对零件(按键)的放置方法也进行了改变,使其放置方法和应该安装的位置相同。 ④ 步行浪费去除的改善 图5-7是一个在音箱板加工工程中将步行浪费去除的例子。 过去的加工方式是将作业者分别配备给每台机器,在存在半成品库存的情况下进行作业。不用说,这种状态完全没有考虑“反应时间”,从V切割机到最后做出完成品的节拍为33秒。 ·人员3名 ·半成品库存约100枚 ·每枚的做出节拍33秒 ·每枚的工时为77秒 1次改善将从物品流动的基本结构彻底改变开始。由于V型切割机沉入地面安装,无法移动。于是,将直割机尽可能向V型切割机移动。本来希望直割机和V型切割机能离的更近一些,但改善的时候,只有在现场亲自做了才知道结果会怎样。由于直割机的电源线长度不够,并且现场也找不到可代替的电源线。最终,只将布局做了部分改变。
下一步,终止三人作业,采用单个流动的多功能持有方式。自然,在直切机和V型切割机之间不会产生半成品。很幸运,员工A是熟手,按照作业指示,很快就习惯了单个流动的作业方式。这时,因为V型切割机和直切机实现了自动传送,进一步施行了人和设备分离的离人化作业方式。通过这些改善,得到如下结果。 ·人员变成1名 ·半成品库存只有3枚 ·周期时间达到35秒 但是,作业的动作路线过于复杂,并且,在复杂的地方会出现浪费。要知道“简单才是最好的”。数一下步行数目,共计有25步,可以认为每走一步浪费1秒钟的时间。将这种情况作为重点,在现场再次开始改善活动。 在2次改善中,设备布局已经有了大的变化,所以从对设备布局做小量调整开始。电源线的长度已达到最大,无法再移动直切机。但是滚筒传送带由于没有电源线,应该可以移动。因此,继续加大滚筒传送带的倾斜度,使其进一步接近V型切割机。 但现场反映说:“如果就这样的话,工件从直切机出来后会掉落在地上。”真的会掉在地上吗?试一试。 掉落在地上了。 一枚网板因此成了不良品。那么怎么办呢?立刻在现场寻找智慧,暂时先在滚筒传送带的边缘加装一块挡板,使工件无法掉在地上。结果成功了,工件顺利沿着传送带开始流动了。 然后,对工件的放置方法进行改善,使工件放置时不会偏离物品的流动方向。这样做,至少减少了工件投入直切机时的一步动作。 最后,将复杂的作业者移动线路简化,为了实现作业动作的流水化,给V型切割机加工完成后的工件设置一个临时放置场,更改作业顺序。通过这些办法,和一次改善后的结果相比,步行数变为17步,减少了8步。周期时间也由原来的35秒缩短为30秒。 和改善前相比,结果如下所示。 ·人员1名(削减了2名) ·半成品库存4枚(削减了96枚) ·做出1枚的节律周期时间30秒(减少了3秒) ·1枚的总工时30秒(减少了43秒) 由于1次改善和2次改善都是在现场即刻进行的,因此,没有花费较多的时间。改善费用为零,要知道,改善费用的大小和研究改善所用的时间是成正比的。 ------------------------------------------------------------------------------------------------------------------ 温馨提示:获得更多分享方法: 1、 打开微信-朋友-添加朋友-查找众账号-精益大本营 2、 点击标题下的"精益大本营"可直接添加关注!如果您觉得"它"还可以,请推荐给同事吧!人人参与才是精益的终极追求。 3、点击右上角-分享到朋友圈,让更多朋友关注精益、关注精益大本营!再次感谢您的关注!谢谢!! 4、点击精益大本营微信平台内右上角小人,可以查看历史所有全部文章 精益大本营是由一群从事精益生产、ie和企业管理的热心朋友所组织,致力于中国工业发展而相互学习帮助和问题讨论,希望我们的精益推送文章能够新老朋友一些帮助。 我们的qq群号是:176343137 更多内容请点击原文阅读。
回复1查看历史丰田物流文章 回复2查看历史看板文章 回复3查看历史活动组织 回复4查看tpm相关文章 回复5查看最新活动内容 回复6查看TQM文章
|