本文回顾了艾利·M.·高德拉特和杰夫·考克斯在1984年出版的著作《目标(TheGoal)》中所表述的约束理论(TOC),同时将它与詹姆斯·P·沃麦克与丹尼尔·T·琼斯在1996年出版的《精益思想(LeanThinking)》中所表述的精益思想进行比较。
1什么是约束理论?
约束理论是一个关注提高企业利润的组织变革方法,它的基本理念是,在任何一个组织中都存在至少一个约束。所谓约束,指的是任何制约该组织获得更多它想获得的东西的因素,对于企业来说,最想获得的东西通常是利润。《目标》一书主要关注制造型企业生产过程中的瓶颈环节这一约束。当然,现实中还存在很多非生产的约束,如市场需求不足,或者销售部门将市场需求转换成订单的能力不足等。
TOC提供了一系列工具,供变革代表们使用,从而管理约束,并帮助提升利润。大多数企业都可以看作是一系列“能将输入转换成能在市场上销售的输出”的相互关联的流程系统。TOC构建了有一个概念模型,即:这个流程系统可以被比喻成链条,并进而借用大家都熟悉的那个道理,“一个链条的强度,取决于它最弱的那一环。” 高德拉特定义了一个5步法流程,变革代表可以使用它来加强链条中最弱的那一个或者几个环节。在《目标》一书中,高德拉特证明了,在大部分组织中,真正意义上的约束其实很少。由于需要关注的重点只是那些真正的约束,所以,实施TOC方法带来的好处是,不需要花费大量的资源就能带来可持续的改进效果,通常3个月左右的时间就能取得显著的改善。
TOC的五个步骤 1.识别系统中的约束环节 系统中构成约束的部分,是其最薄弱的环节,它可能是实体形式的,也可能是制度(政策)形式的。 2.决定如何最大限度地利用约束环节的能力 高德拉特教导变革代表们,要在不进行昂贵的改造和升级的前提下,最大限度地释放出约束环节的能力。 一个例子是,减少乃至消除瓶颈环节生产设备的停机时间。 3.其余的一切都应服务于约束环节 系统中所有的非约束环节,都应该围绕保证约束环节的最大化效能而运作。当这一步完成之后,需要确认约束是否转移到系统内的其它环节。如果确认约束已经被消除了,则变革代表可以直接跳到第5步。 4.提升约束环节的能力 所谓“提升”约束环节的能力,就是采取一切必要的行动,从根本上消除约束。只有在第2步和第3步未能凑效的情况下,才需要考虑该步骤。在这一步,可以考虑对于现有系统进行大力度的改造。 5.回到第1步,但得小心别让“惰性”成为约束 实践者们可能在实施TOC的过程中逐渐变得自满,高德拉特对此提出了特别警示。TOC是一个持续进行、永无终点的过程,满足于已经取得的进步而产生的惰性,将会成为持续进步的障碍。
高德拉特还设立了一套推进变革过程的指标系统,包含3个衡量指标,并藉此为通过TOC实现组织变革提供了一个基础。他非常正确地认识到,传统的会计体系并不支持TOC,或者精益相关的改进努力。高德拉特建议,替换掉传统会计学中所有由“生产成本”会计范式相关的衡量指标。TOC认为,要驱动真正的利润增长,必须采用下面这套新的衡量指标:
1.有效产出(Throughput) 该指标指的是,整个组织通过出售产品或服务来获得金钱收入的速度。有效产出表示了整个组织获得的所有收入。 2.库存(Inventory) 该指标指的是,整个组织为将来要销售的东西,而进行的所有投入。库存表示所有还停留在组织内部的金钱的总和。高德拉特所谓的“库存”,不仅包括原材料,在制品及成品,还包括各种设施,设备,以及暂时不需要的东西。 3.运营费用(Operating Expense) 运营费用是指将“库存”转变成“有效产出”所花费的钱。它表示组织在运作过程中的付出。直接人工成本,水电气费,消耗品,以及固定资产的折旧,都是“运营费用”的组成部分。 这三个衡量指标是相互关联的。这意味着,当其中一个指标发生变化时,将会导致另外两个指标中至少一个的变化。因此,在使用TOC来提高你企业的绩效时,变革代表需要铭记以下准则:
最大化有效产出的同时,降低库存和运营费用 这三个指标是日常决策过程中最主要的参考。高德拉特主张,所有的改善机会都应该按照对这三个指标的影响大小来定义其优先级,尤其是对有效产出的影响,而有效产出在理论上仅受整个市场规模的限制。
2精益思想与约束理论的对比
和约束理论一样,精益思想也是一个用来提高企业利润的组织变革方法。精益思想起源于日本,并且在丰田生产方式中得到了极致的体现。日本的制造业在二战之后深受各种约束的影响,丰田公司的大野耐一先生为了突破这些约束,建立了一个要远好于大批量生产方式的新的制造体系。与大批量生产的制造方式相比,精益生产只需要近乎一半的人力、场地、库存及产品开发时间。同时,它还能实现更高的质量水平,及更多的产品品种。精益生产的这些优势,会导致企业销售额的提升,并进一步为释放出的企业资源提供了出路。《精益思想》一书通过对丰田生产方式的理论化解读及扩展,使其也适用于非制造型的组织,以及产品开发过程。
和TOC一样,精益思想的目的也是提高企业的利润。这一目的,是通过降低下列等式中的“成本”来实现的: 利润= 售价-成本 丰田意识到,售价是由市场决定的,企业不能自由提价。于是,唯一能够提高利润的办法就是降低成本。请注意,尽管高德拉特试图避开降低成本的话题,而强调提高有效产出,但是最后的结果如出一辙:由于成本的下降带来利润的提升。
精益思想实现成本降低的方法是,强调企业组织作为一个系统,应该致力于创造客户认可的价值。精益的努力,应该致力于消除产品和服务提供过程中所有不为最终客户增加价值的步骤。
精益思想也有5个步骤:
1.从客户的视觉来定义价值 2.识别价值流 3.流动 4.拉动 5.追求完美
约束理论从找出约束着手,而精益思想则告诉变革代表从重思什么是客户认可的价值开始。通过现场观察整个价值流,典型的是从成品回溯到原材料,不断地质疑自己:“我们的客户愿意为这项成本买单吗?”精益变革代表可以识别出系统中存在的、能够消除浪费的机会。另外,价值流图析(VSM)是一项强大的工具,有利于确定整个系统中哪些地方需要首先被改善。与此同时,对未来状态价值流的规划也能帮助整个组织更好地聚焦在共同的目标方向上。
精益思想和约束理论都认为,一个组织要先找到需要改变的地方,然后再决定是不是需要请一位老师来教自己。《目标》一书中虚构了一个叫做Jonah的老师角色,在关键点上提供支持。但是,高德拉特反对那种依赖老师的做法,主张变革代表应该在实践中不断学习,成长为老师。同样的观点是,成功的精益实施是建立在不断尝试和犯错的基础之上的,这样才能培养“自己家”的精益老师。然而,需要提醒的是,这种方法往往需要比较长的时间才能取得可观的结果。一个好的老师能够促进变革效果的同时,帮助维持好的变革势头。约束理论宣称,可以在三个月左右实施一轮改善,这在没有老师辅导的情况下是很难实现的。有趣的问题是,按照约束理论来将公司内部的变革代表培养成像Jonah那样的老师,到底需要多少时间呢?
下表总结了精益思想和约束理论的主要对比:
汇总表:约束理论与精益思想的对比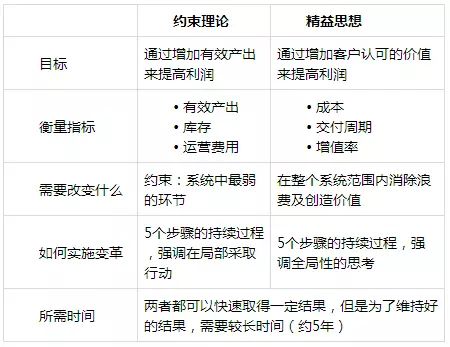
3将精益思想与约束理论结合起来
约束理论能够在精益实施的过程中起到促进作用吗? 笔者认为,答案是肯定的!约束理论的方法可以极好地契合在精益思想5个步骤的框架中,确切地说是在第2步和第3步之间。运用约束理论的方法,可以帮助精益变革代表们在无法彻底消除瓶颈的地方改进其绩效。更确切地说,在规划好将来未来状态价值流图之后,如何来实现它?就像《学习观察学》里面所介绍的那样,当你把价值流图分解成若干个流程环,并为它们制定改善目标的时候,结合约束理论的方法可以在下列这些方面有所帮助:
•决定从哪里开始 TOC主张从最影响有效产出的约束环节开始。这样能够短期内在价值流程上取得较大的改善,有利于激发员工的动力并获得支持。 •维持变革动力 为了达到未来状态的目标,可能会需要设计一些目前市场上还没有被开发出来的新设备。在这些流程环节没有被完全消除之前,如果它们是系统中的约束,TOC可以被用来维持实施的力度。那样,你才可以开发能按节拍时间要求运转的连续流生产单元,控制生产的拉动系统,并实施均衡生产。
•能够支持精益实施的绩效衡量指标 使用高德拉特的三项指标(有效产出、库存和运营费用)来代替传统会计学里面的资产利用率和分摊成本,可以帮助管理层看到精益思想带来的收益。
以上就是关于约束理论的介绍,以及它与精益思想的对比。我们会继续总结一些可能有用的观点,并附在本文之后。
参考书目 Dettmer, William H. Goldratt’s Theory of Constraints A Systems Approach to Continuous Improvement. Milwaukee, Wisc.: ASQ Quality Press, 1997. Goldratt, Eliyahu M. and Cox, Jeff. The Goal. Great Barrington, Mass.: The North River Press, 1992. Goldratt, Eliyahu M. What is this thing called Theory of Constraints and how should it be implemented? Great Barrington, Mass.: The North River Press, 1990. Noreen, Eric, Debra Smith, and James T. Mackey. The Theory of Constraints and its Implications for Management Accounting. Great Barrington, Mass.: The North River Press, 1995. Rother, Mike and John Shook. Learning to See. Brookline, Mass.: The Lean Enterprise Institute, 1998. Womack, James P. and Daniel T. Jones. Lean Thinking. New York: Simon and Schuster, 1996. (感谢志愿者胡俊杰承担了本文的初稿翻译任务,志愿者王劭禹对翻译初稿进行了校订,最后由周健定稿。)
摘自:精益企业
广东精益管理研究院 2015.07.03
|