通公司的习惯→将大扫除当做每年定例仪式来做 vs Toyota的非常识习惯 营造一个即便是想弄脏也不会脏的工作场所
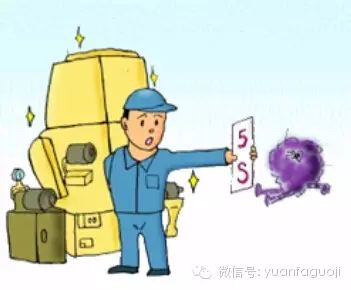
一个企业的“制造力”看仓库就可以明白。比如说是不是做到新人也可以很快可以取出需要的东西的状态,只看这点就可以明白。 整理整顿是十分重要的。所以无论哪个企业每年都会进行一两次的大扫除或整理。大部分的工厂都会贴着“整理整顿”“5S(整理、整顿、清扫、清洁、素养)的彻底”这样的标语。问题是可以彻底到怎样的程度。 5S的起点是整理整顿。所以要扔掉不需要的东西。 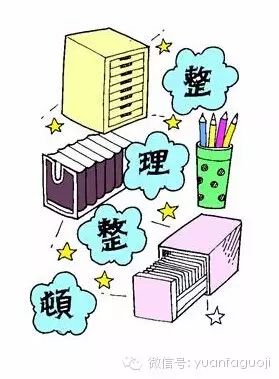
制造力弱的企业的特征是东西会溢出来。那是因为“需要的东西没有,有的净是不需要的东西”。这种状态需要改善。 首先,要将需要的东西、不要的东西、不常使用东西分开明确分开,不要的东西果断处理掉。在企业中有很多不要的东西、工作;这会导致成本上涨;引起时间、人的浪费。 将不要的东西处理掉的话,谁都会惊叹“我们公司真宽敞啊”。但是,如果还是按照之前的放置方法的话,瞬间就会被打回原形。 将每一个产品都进行定位管理,什么东西在哪有几个设置成很快就可以明白的状态。“明白”的基准不是担当者、老员工、而是要刚入社的新员工。 整理整顿到位以后,下面是清扫清洁。清扫,实现没有污物、垃圾的工作场所。做完以后大家就会松了一口气觉得“变干净了呢”。 但是,在很多企业中这种“变干净了呢”的状态不会长期持续。物品的放置方法也会变得不被遵守。脏污、垃圾又会重新浮现在眼前。过了半年又会觉得“好杂乱啊,再做一遍5S吧”这样的事例屡见不鲜。 但是,丰田式的思考方式认为,将5S作为定例重复的“仪式”是绝对不可以的。丰田式标榜的是营造一个“即便是想弄脏也不会脏这种程度工作环境”“即便是想找东西也没必要找这种程度的工作环境”。 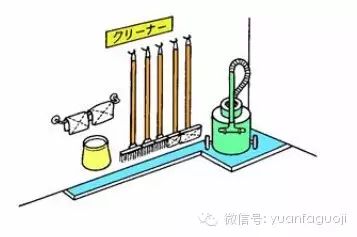
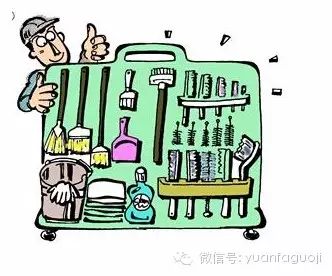
以丰田式为基础进行生产改革的F社,实现了5S以后,为了保持下去无论清扫多少遍也会很快会有脏污、垃圾非常显眼,于是对原因进行了彻底的究查。 然后,发现原因是零件的过剩包装。F社每天要拆解大量产品包装,这个时候出现很多垃圾,这就是原因。 过剩的包装是废弃物浪费,成为了垃圾,污染了公司,拆解包装的时间也是一种浪费。F社为了改变“刻意花钱买浪费”的状况,不断进行了改善,比如使用可以多次使用的周转箱收纳部品。 在此基础上将工厂、事务所的地面、墙壁设置了A2大小的区划。设置了员工也好、董事也好,全体出动的时间。每天停线15分钟,全员进行扫除。某个意义上来说,这时间很“浪费”,但是为了将自己的工作岗位自己保持整理整顿这个意识进行彻底是不可欠缺的。 就这样F社成功营造了一个几乎没有脏污、垃圾的工作场所。制造力也随之增强了。 Toyota的非常识习惯→自己的工作岗位自己整理整顿。
|